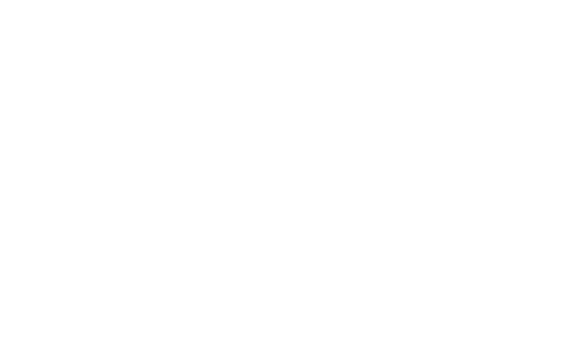
Improving Operational Efficiency: Best Practices for Streamlining Your Business Workflow
Operational efficiency is a critical factor that impacts every aspect of your business—from productivity and profitability to customer satisfaction. In today’s highly competitive market, businesses are constantly looking for ways to streamline their operations, minimize waste, and maximize output. Improving operational efficiency not only helps cut costs but also enhances the ability to scale and adapt to market changes.
This article will guide you through some of the best practices for improving operational efficiency in your business workflow. Whether you're a startup or a well-established enterprise, these strategies can help you eliminate inefficiencies, boost team performance, and improve your bottom line.
Streamlining business processes requires a combination of strategic planning, process optimization, technology adoption, and employee engagement. By implementing these best practices, businesses can achieve higher productivity, lower operational costs, and deliver exceptional value to customers. Let’s explore these best practices that will enable you to take your operational efficiency to the next level.
Understanding the Importance of Operational Efficiency
Operational efficiency is about optimizing resources to produce the maximum output with minimal input. Improving operational efficiency can help businesses:
Increase Profitability: By reducing waste and improving productivity, businesses can lower their operational costs, leading to higher profit margins.
Enhance Customer Satisfaction: Efficient operations lead to faster response times, better product quality, and more reliable service, all of which increase customer satisfaction.
Support Growth: Efficient businesses are better equipped to scale operations without a proportional increase in costs. By streamlining processes, businesses can expand without sacrificing quality or customer service.
For example, consider a company that manufactures consumer goods. By optimizing its production line, the company can increase its output without hiring additional employees or investing in new equipment. This improvement in efficiency results in more products being made with the same amount of labor and resources, thus boosting profitability.
Best Practices for Improving Operational Efficiency
Identify and Eliminate Bottlenecks: The first step in improving operational efficiency is identifying bottlenecks in your processes. Bottlenecks are areas where work slows down, leading to delays and wasted resources. These might occur in manufacturing, customer service, or even in administrative tasks.
To identify bottlenecks, perform a process audit. This involves reviewing all business operations, mapping workflows, and talking to team members to understand where delays occur. Once identified, you can work on resolving the issue. For example, if a certain department is overwhelmed with tasks, consider redistributing workloads or investing in automation tools to speed up the process.
Another effective approach to eliminating bottlenecks is the Theory of Constraints (TOC). This management strategy focuses on identifying the single constraint that limits a business's overall performance and finding ways to eliminate or mitigate it.Standardize Processes: Standardizing processes is one of the most powerful ways to improve operational efficiency. When tasks are standardized, they are performed consistently, which reduces errors, increases speed, and ensures quality.
For instance, developing Standard Operating Procedures (SOPs) for routine tasks helps ensure that every employee follows the same steps. This reduces variability and streamlines operations. SOPs should cover all essential processes, from order processing and inventory management to customer service protocols and employee onboarding.
Standardization also makes it easier to onboard new employees, as they have clear guidelines to follow. This leads to faster training times and fewer mistakes, further improving efficiency.Leverage Technology for Automation: Technology is a game-changer when it comes to operational efficiency. Automation tools can streamline a wide range of tasks, from administrative functions to customer service.
A simple example of automation is the use of email marketing platforms. Instead of manually sending promotional emails, businesses can set up automated email campaigns that run on a schedule, targeting specific customer segments based on their behavior.
Another example is inventory management software, which automatically updates stock levels in real-time, places reorder requests, and helps businesses maintain optimal inventory without manual intervention.
By adopting tools that automate repetitive tasks, businesses can reduce human error, save time, and improve overall efficiency. Automation doesn’t require large investments and is accessible to businesses of all sizes.Empower Employees through Training and Collaboration: Efficient businesses rely on skilled and knowledgeable employees. Investing in training programs ensures that employees understand the best practices and tools available to them, enabling them to work more efficiently.
For example, cross-training employees in different departments or roles helps increase flexibility within the workforce. If one department is behind, a cross-trained employee can step in to assist, preventing delays and bottlenecks.
Additionally, fostering a collaborative environment can significantly improve efficiency. When employees have access to the right tools and resources, they can work together seamlessly, share insights, and resolve problems quickly. Tools like Slack or Microsoft Teams can facilitate communication and collaboration in real-time, ensuring everyone is aligned and working toward the same goals.Focus on Continuous Improvement: Operational efficiency isn’t a one-time goal; it’s an ongoing process. Successful businesses regularly evaluate their processes and look for areas to improve. This concept is known as Kaizen, a Japanese philosophy that emphasizes continuous, incremental improvement.
To implement Kaizen in your organization, establish a system for regularly reviewing your operations. Set up feedback loops that allow employees to suggest improvements, and encourage them to be proactive in identifying areas where efficiency can be enhanced.
Additionally, track performance metrics to measure the success of improvements. Key Performance Indicators (KPIs) such as cycle time, output per employee, and cost per unit help determine if the changes are making a meaningful impact on efficiency.
The Role of Data Analytics in Operational Efficiency
Data analytics plays an essential role in driving operational efficiency. By leveraging data, businesses can make informed decisions that optimize processes and drive better outcomes.
For instance, predictive analytics can help businesses forecast demand and adjust production schedules accordingly. This reduces the risk of overproduction or stockouts, ensuring that resources are used effectively and efficiently.
Data dashboards provide real-time insights into various operational areas, such as inventory, sales, and customer feedback. These dashboards allow businesses to track key metrics, monitor progress, and identify any potential issues before they become problems. With the right data, businesses can optimize workflows, reduce inefficiencies, and make data-driven decisions that improve productivity.
Conclusion
Improving operational efficiency is essential for businesses looking to stay competitive, reduce costs, and enhance customer satisfaction. By identifying bottlenecks, standardizing processes, leveraging automation tools, empowering employees, and focusing on continuous improvement, businesses can significantly enhance their efficiency and profitability. Furthermore, using data analytics to track and measure performance allows businesses to make informed decisions and ensure that their operational improvements are yielding the desired results.
Implementing these best practices requires strategic planning, a commitment to innovation, and ongoing effort. However, the rewards are substantial: increased productivity, better resource allocation, and improved customer satisfaction. Operational efficiency isn’t a one-time fix—it’s a continuous journey that will drive success in your business for years to come.
By following the best practices outlined in this article, businesses can optimize their workflows, enhance performance, and achieve lasting growth and profitability.